Protecting your waterfront property against erosion is a top priority. Seawall panels are designed and built to withstand a great deal of force. Think about the strength of ocean waves crashing up against seawalls day in and day out. They are also exposed to every outdoor element, and therefore must be resistant to rust and corrosion.
Related Blog: How a New Seawall Can Increase the Value of Your Home
Seawalls are a critical part of any waterfront home or business. They serve to prevent eroding of the land which will naturally occur over time if not protected. If left unprotected, eventually this can lead to damage of property. Seawalls are your most important line of defense and are most commonly made out of concrete. You may be wondering how these massive structures are built. Let's delve into the world of concrete seawall manufacturing.
Where Are Seawalls Made?
A seawall is not one continuous piece. In fact, seawalls are made of panels which are then assembled at the site. It comes as no surprise that seawalls are not made on site. It is a process, involving several steps, taking over half a month to make one panel. In fact, these massive structures are made off-sight in large manufacturing yards. It takes a great deal of space and heavy equipment to make and transport seawall panels.
Materials Need to Make Seawall Panels
The size of the panels will determine the amount of material needed. Ten-foot panels are the most common size for a seawall panel, but other sizes are available if needed. Steel rebar is used to create the steel mat. The steel used is low carbon and is corrosion resistant. This is important since a good portion of the wall will be submerged in water. The purpose behind the steel mat is to lengthen the life of the seawall. Concrete is the main material used in seawalls. It's not just your ordinary patio concrete. The concrete used is a special marine grade 5500 PSI mix which is stronger than concrete used for residential purposes. The most common material used for the weep holes of seawalls is PVC pipe.
The Process of Making Seawall Panels
The first step in making a seawall panel is to make the steel mat. Once the steel mat is constructed and tied together it is placed in a form. The form helps keep the shape of the panel, until the concrete sets. A utility chair is used to center the steel mat in the center panel, otherwise, it would sink to the bottom of the form decreasing its effectiveness.
Next, concrete is poured into the seawall form and smoothed out. Finally, PVC pipes are inserted to make the weep holes. Like most products manufactured, seawalls panels are stamped with the date they were manufactured. Seawalls are designed to last for many years. A property may change hands multiple times before the seawall needs repairing or replaced. The manufactured date makes it possible to know the age of the panel no matter how many times ownership has changed.
Once the seawall is finished, it must set for at least 14 days. This period of time is necessary to allow the concrete to set and cure. Allowing it properly cure allows the panel to reach its maximum strength.
Only the Best
Even though it seems like a long process just to create one panel, think of the service that seawalls provide. They must be strong because they endure harsh elements. When installing your seawall, you want to make sure you use only the most well-constructed panels installed by seawall installation experts. Duncan Seawall has years of experience and offers professional installation of both residential and commercial seawalls using only the highest-quality seawall panels available.
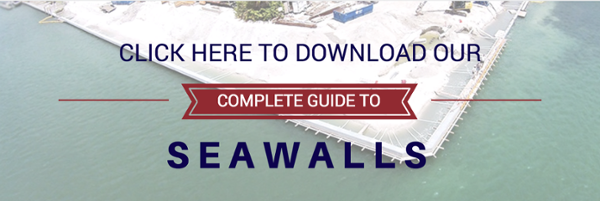